Plastic Film
Home > plastic film
Table Of Contents For This Page
It is not easy to introduce all complete information of spunbond non woven fabric, here we have classified the information that you may interested on this page. Please click the below content, and find the information which you are most interested. You also could detailed reading all the information from top to bottom on this page, which might take you about 10-20 minutes.
Hot Selling Prodcuts
Hefei Medpos is a leading manufacturer of sanitary material in China. With over 10 years experience and close cooperation with our partners, we can provide you all your needs with an affordable price! Our products include spunbond, SMS, spunlace non woven fabric, plastic films and PE laminated materials.
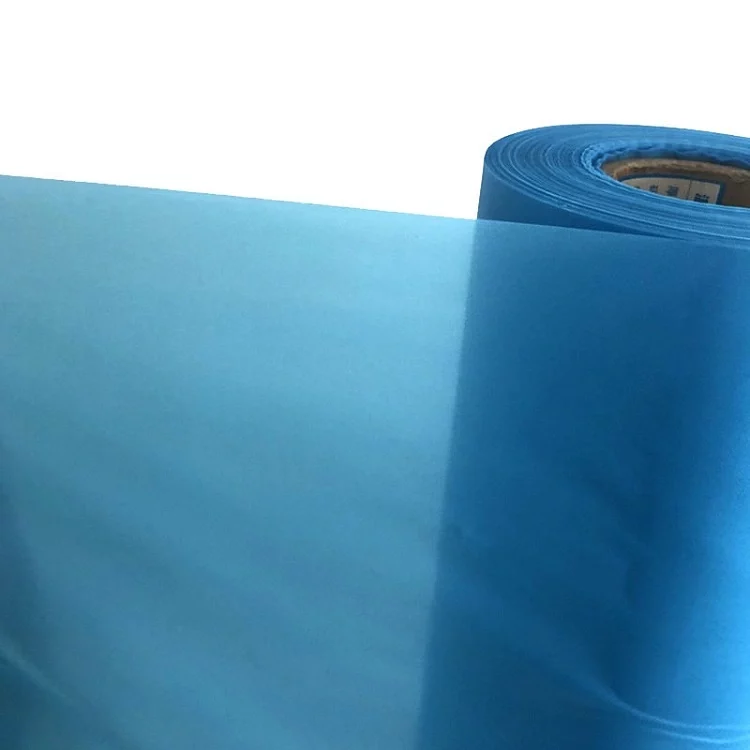
Cast Film
Material: PE/PP/PVC/PET
Size: 10-260cm
Weight: 10-100gsm
Color: Blue, Green, White or Customzied
Type: Single Layer Extrusion/Multi-layer Coextrusion
Packing: As request
Application:
-Hygiene Products: Backsheet film of baby diaper, adult diaper, sanitary napkin, under-pad
-Daily Products: gloves, shoe covers, caps, table cloth, apron, bedsheet etc.
-Healthcare Products: protective gown, surgical gown, isolation gowns, medical drapes, disposable coveralls
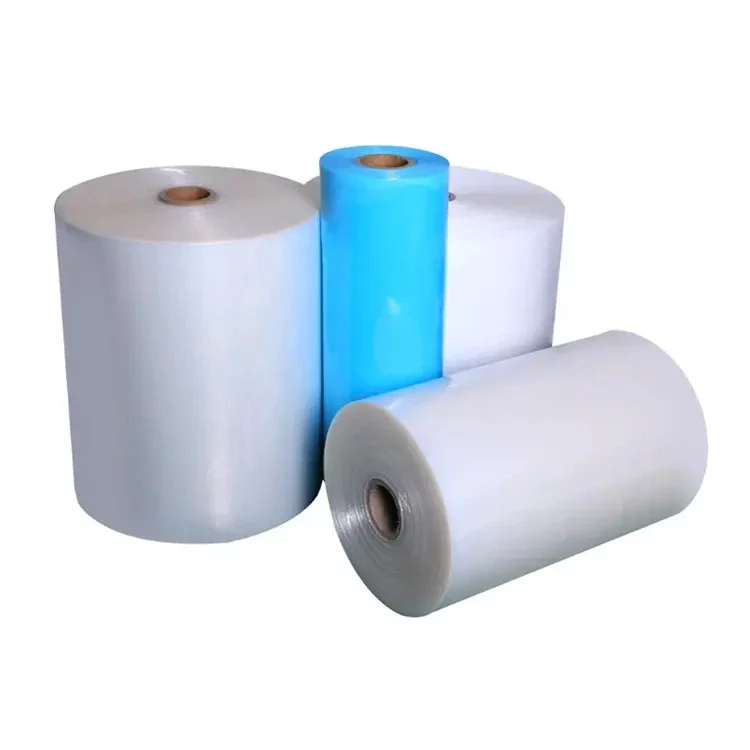
Blown Film
Material: PE/PP/PVC/EVA
Size: 10-260cm
Weight: 10-100gsm
Color: Blue, Green, White or Customzied
Type: Blown Extrusion
Packing: As request
Application:
-Packaging films: shrink film, stretch film, bag film, container liners, and laminating film
-Medical Consumables: dental bibs back–sheets, mayo stand cover and etc.
All You Need to Know About Plastic Film
What is Cast Film?
Cast film refers to a type of film manufacturing process where a thin film is created by extruding a melted polymer through a flat die onto a polished chill roll. This process produces a continuous, thin sheet of film with consistent thickness and excellent clarity.
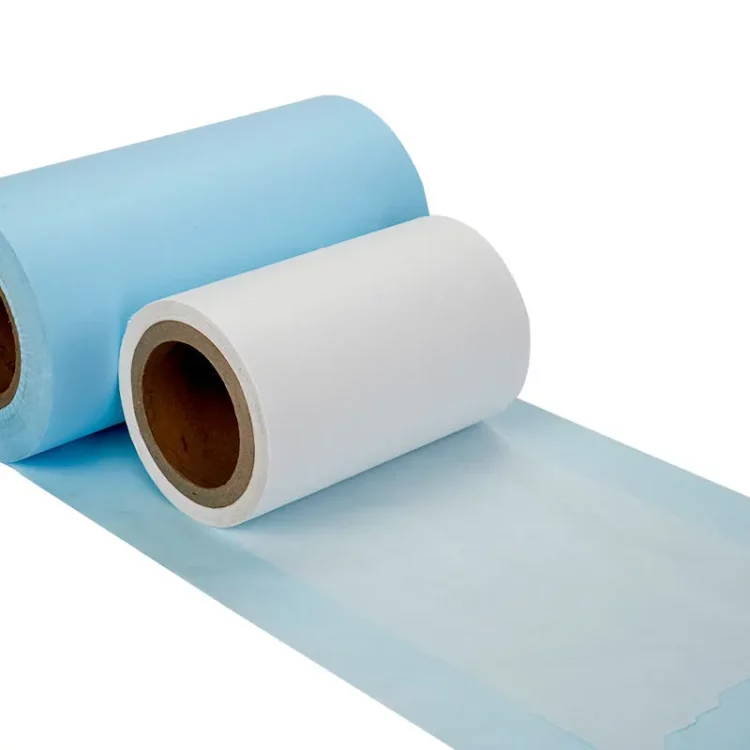
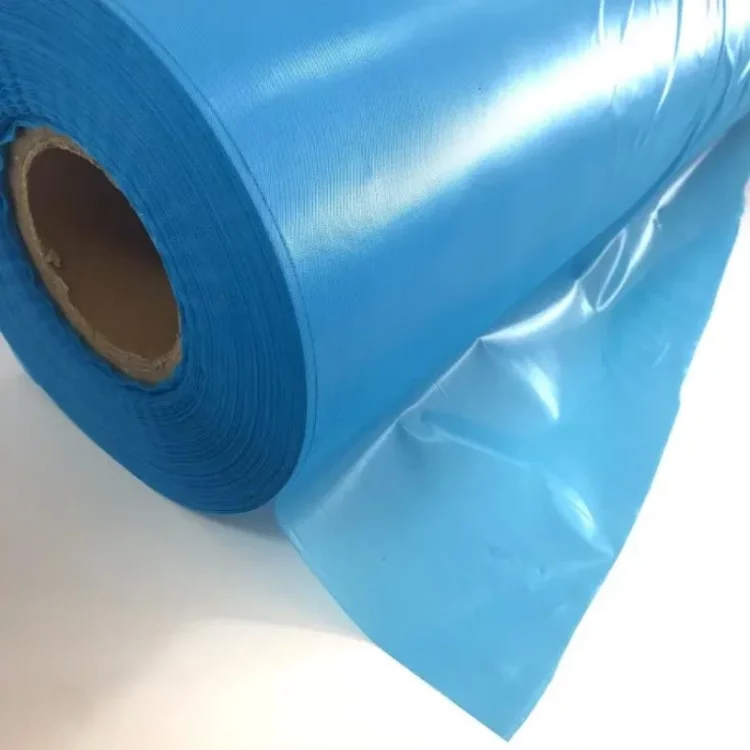
What Are The Characteristics of Cast Film?
Good Barrier Properties: Many cast films can be engineered to provide excellent barriers against moisture, oxygen, and other gases, which is crucial for food packaging and other protective applications.
Excellent Optical Clarity: They often have high transparency, making them suitable for applications where visibility or product presentation is important.
High Gloss: Cast films typically have a glossy surface, enhancing the appearance of printed graphics and making them attractive for retail packaging.
Good Mechanical Properties: They offer good tensile strength and tear resistance, providing durability and reliability in use.
Uniform Thickness: Cast films are produced with a consistent thickness, which is essential for applications requiring precise material properties and performance.
What is Blown Film?
Blown film is another method of manufacturing plastic films, distinct from cast film. In blown film extrusion, plastic resin pellets are melted and extruded through an annular die (a circular die with a hole in the center) into a tube. This tube of molten plastic is then inflated (or “blown”) with air to expand its diameter while it continues to cool and solidify. Finally, the tube is flattened and wound onto rolls as a continuous film.
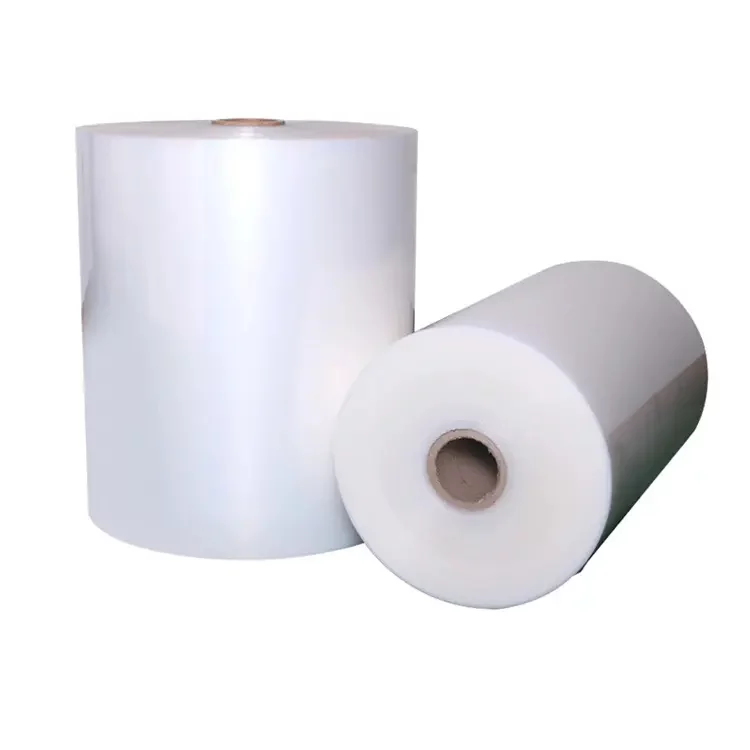
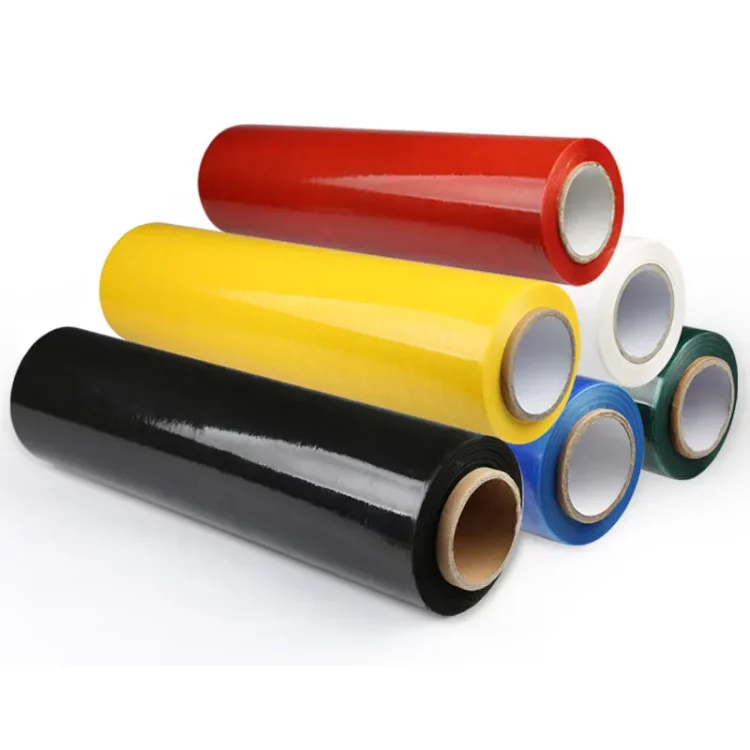
What Are The Characteristics of Blown Film?
Strength and Puncture Resistance: Blown films typically exhibit good strength and puncture resistance, making them suitable for applications where durability is important.
Flexibility: They can be manufactured to be relatively flexible, which is advantageous for applications requiring the film to conform to shapes or be easily manipulated.
Barrier Properties: Like cast films, blown films can be engineered to have good barrier properties against moisture, oxygen, and other gases, depending on the specific resin used and manufacturing conditions.
Versatility in Applications: Blown films are used in various industries, including packaging (such as bags, liners, and wraps), agriculture (greenhouse films), and industrial applications (protective covers and liners).
Variety of Thickness: Blown films can be produced in a wide range of thicknesses, from very thin films to thicker sheets, depending on the application requirements.
What Are The Differences Of Cast Film and Blown Film?
Manufacturing Process
Cast Film: Process: Involves extruding melted polymer through a flat die onto a chill roll.
Blown Film: Involves extruding melted polymer through an annular die to form a tube, which is then inflated with air to expand its diameter.
Characteristics
Thickness: Blown films can vary more widely in thickness than cast films, which are generally produced with a very consistent thickness.
Clarity: Cast films often have better optical clarity and surface gloss compared to blown films.
Mechanical Properties: Blown films tend to have better impact strength and puncture resistance, while cast films may have better tensile strength and tear resistance.
Applications
Cast Film: Commonly used in applications requiring high clarity, consistent thickness, and smooth surface finish, such as food packaging films, labels, and lamination films.
Blown Film: Suitable for applications requiring toughness, flexibility, and variability in film thickness, such as trash bags, agricultural films, and heavy-duty packaging.
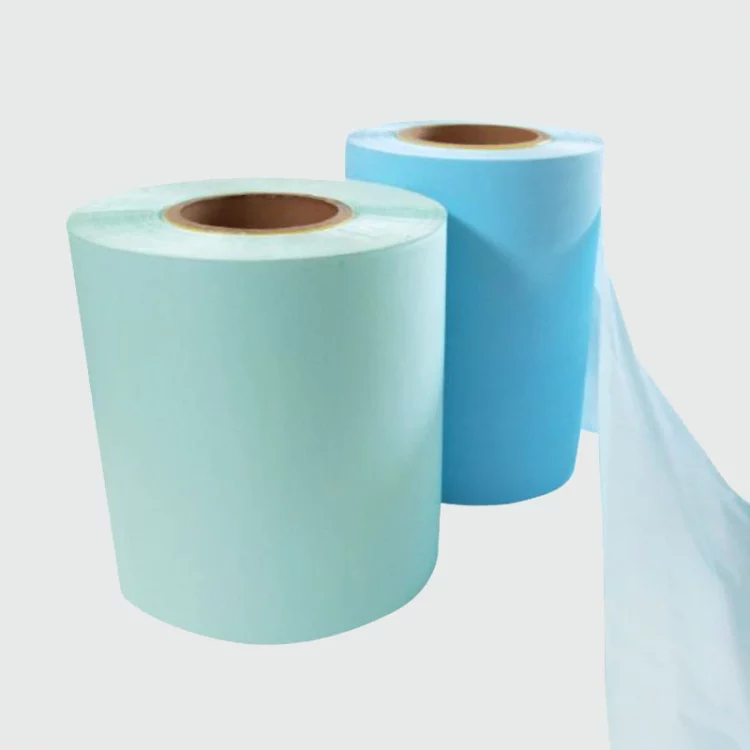
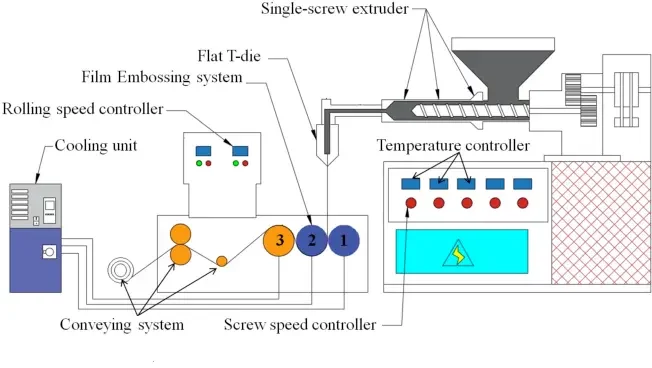
What Is The Production Process of Cast Film?
1.Resin Handling and Extrusion
Resin Selection: Choose the appropriate type of polymer resin based on the desired properties of the film, such as polyethylene (PE), polypropylene (PP), or other specialty resins.
Melting: The resin pellets are fed into an extruder where they are heated and melted to a precise temperature suitable for extrusion.
2.Extrusion through Flat Die
Extrusion: The melted resin is forced through a flat, slit die with a uniform gap to form a continuous sheet of molten polymer.
Die Adjustment: The die gap is adjusted to control the thickness of the film as it exits the die.
3.Cooling on Chill Roll
Chill Roll: Immediately after exiting the die, the molten polymer sheet is rapidly cooled and solidified by contact with a chilled, polished steel or chrome roll.
Cooling Process: The rate of cooling and the temperature of the chill roll are carefully controlled to achieve uniform solidification and desired film properties.
4. Orientation and Stretching
Machine Direction (MD) Orientation: As the film is pulled away from the chill roll, it undergoes some orientation in the machine direction (MD) due to the stretching effect.
Transverse Direction (TD) Orientation (Optional): Some cast films may undergo additional stretching in the transverse direction (TD) through a secondary process to enhance mechanical properties.
5.Winding
The winding process is to wind the cast film to a certain width and length for subsequent processing and transportation. The winding machine is usually operated by an LCD screen and a programmable controller, which can adjust parameters such as size and speed as needed.
What Is The Production Process of Blown Film?
1.Resin Handling and Extrusion
Resin Selection: Choose the appropriate type of polymer resin based on the desired properties of the film, such as polyethylene (PE), polypropylene (PP), or other specialty resins.
Melting: The resin pellets are fed into an extruder where they are heated and melted to a precise temperature suitable for extrusion.
2.Extrusion through Annular Die
Annular Die: The molten resin is forced through an annular (circular) die, which forms a tube-like structure of molten plastic.
Bubble Formation: As the molten resin exits the die, it forms a continuous tube. Air is introduced through a mandrel inside the tube, inflating it to form a bubble.
3.Bubble Expansion
Bubble Cooling: The inflated bubble of molten plastic continues to cool as it moves upward (vertically or horizontally) away from the die.
Bubble Control: The size and thickness of the bubble are controlled by adjusting the rate of air flow and the speed at which the tube is pulled upward (haul-off speed).
4. Bubble Cooling and Solidification
Cooling Ring: A cooling ring or system of air jets cools the outside of the bubble to solidify the molten plastic into a stable film structure.
Thickness Control: The thickness of the film is controlled by adjusting the extrusion rate of the resin, the air pressure inside the bubble, and the rate of cooling.
5.Bubble Collapse and Flattening
Collapsing the Bubble: Once the desired film thickness is achieved and the film has cooled sufficiently, the bubble is collapsed by pulling it through a pair of nip rollers.
Flattening and Winding: The flattened tube of film is then wound onto rolls for further processing or packaging.
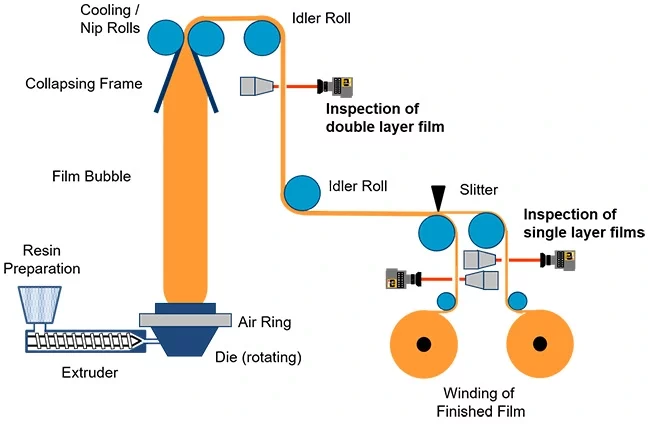
Applications
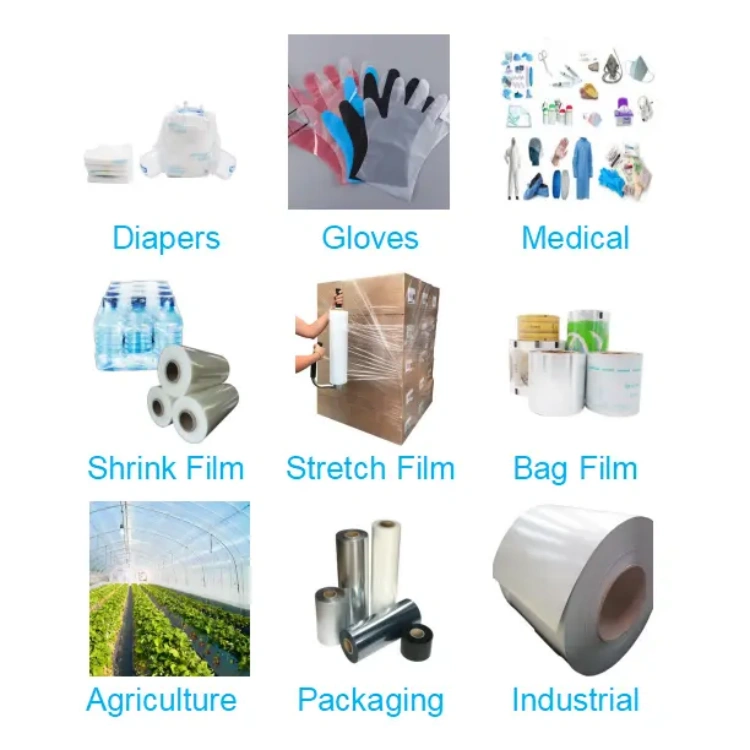
Packaging
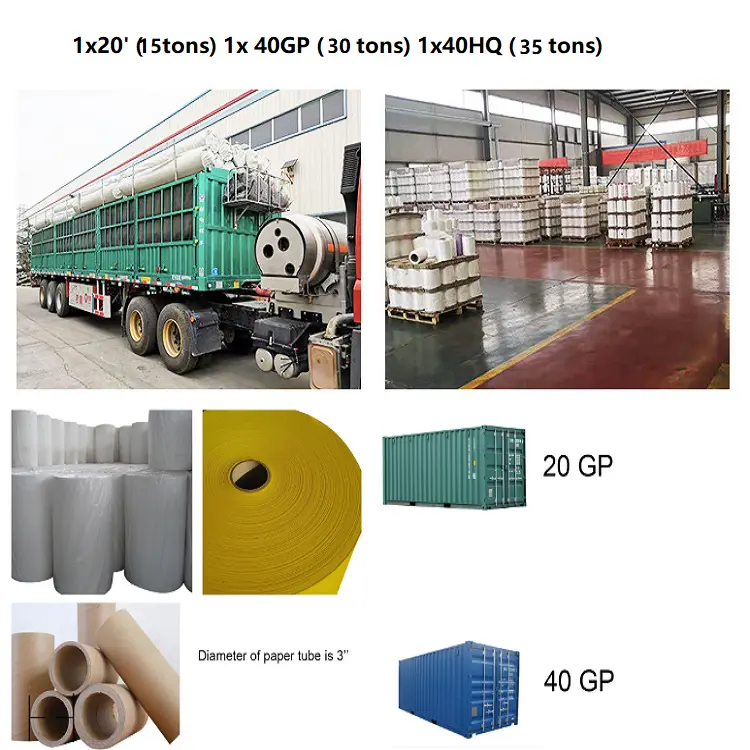
Considerations When Bulk Purchase Plastic Film
When bulk purchasing spunbond non-woven fabric, thorough research and due diligence are essential. Focus on material specifications, supplier reliability, quality standards, and application requirements while also considering cost, logistics, and environmental factors. This comprehensive approach will help ensure you select the right product and supplier for your needs. Here are elaborations of some key considerations:
1. Material Specifications
•GSM (Grams per Square Meter): Determines the fabric’s weight and thickness. Higher GSM indicates a thicker and stronger fabric.
•Material Composition: Commonly polypropylene, but other materials like polyester or polyethylene might be used depending on the application.
2. Quality and Standards
•Manufacturing Standards: Ensure the fabric meets industry standards and certifications.
•Quality Control: Verify the manufacturer’s quality control processes and request quality certificates or test reports.
3. Supplier Reliability
•Production Capacity: Ensure the supplier can meet your bulk order requirements within the desired timeframe.
•Sample Request: Obtain samples before placing a large order to verify quality and suitability.
4. Technical Properties
•Strength and Durability: Confirm the fabric’s tensile strength, tear resistance, and durability.
•Permeability: Ensure the fabric meets your needs for breathability and moisture vapor transmission.
•Barrier Properties: Assess resistance to water, chemicals, and other potential contaminants if applicable.
5. Application Requirements
•Intended Use: Match the fabric’s specifications to the specific requirements of your application, whether it’s for medical, agricultural, industrial, or hygiene use.
•Customization: Determine if the supplier offers customization options such as specific sizes, colors, or treatments (e.g., anti-bacterial, anti-static).
6. Cost and Logistics
•Pricing: Compare prices from multiple suppliers, considering not just the cost per unit but also shipping and handling fees.
•Minimum Order Quantity (MOQ): Ensure the supplier’s MOQ aligns with your needs.
•Delivery Time and Logistics: Confirm lead times, shipping options, and logistics arrangements to ensure timely delivery..
7. Environmental Considerations
•Sustainability: Inquire about eco-friendly options or recycled materials if sustainability is a priority.
•Disposal and Recycling: Understand the disposal and recycling options for the fabric after use.
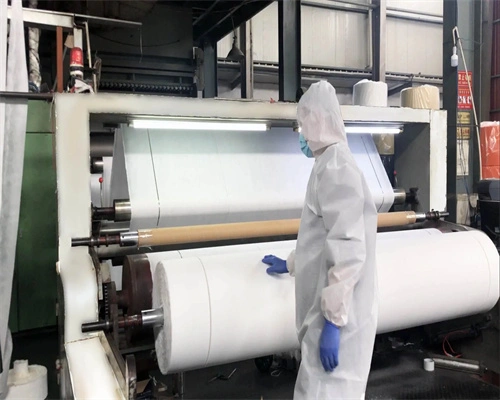
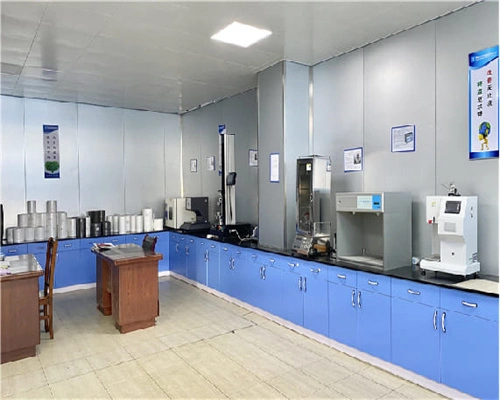
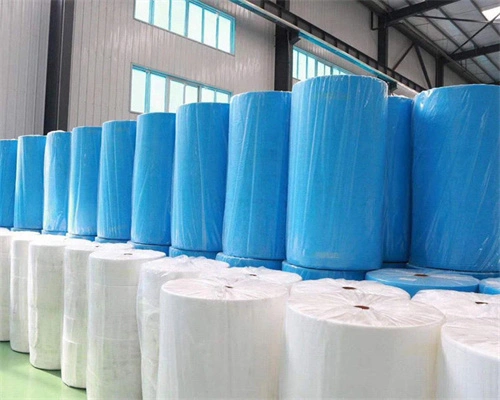
With more than 10 years’ production and export experience in the sanitary material field, we are pround to say all requirements above are statisfied by Medpos. We are always providing stable and competitive price, consistent quality, on time delivery, 24/7 timely response and professional service. And we will make efforts to minimize your purchasing and shipping costs and provide options for your choice if need.
Work Process & Duration Estimation
Working with Medpos will be more efficient. We only take your 1% time to finish 20% of your workload!
Inquiry & Quote (1~3days)
After receiving customer inquiry and studying requirements, we will provide with an accurate quotation within 24 hours. Prices are generally valid for 20 days due to fluctuation of raw materials.
Samples (3-7days)
We have stock sample for normal width and weight in small quantity. For custmoized samples, it takes 3-7 days to produce according customer need such as weight, width and physical performance.
Bulk Production (15-30 days)
Our bulk production time is generally 15 to 30 days. Raw material normally takes 5 to 10 days. After the material arrives at the factory, our quality inspection department will inspect materials at first, then start mass production after passing the test.
Secondlly, we will make pre-production sample to ensure quality in line with customer requirements.
Thirdly, during mass production, our quality inspection department will also conduct several random inspections. The bulk production time is around 10-15 days.
At last, our quality inspection department will conduct the last inspection when mass production is finished.
Delivery (1 day)
Once production approved by our end or the third party. We will make the shipment immediately to ensure client receiving the goods at the earliest time.
A Brief Self-Nomination ,Why Choose Hefei Medpos?
Hefei Medpos is a specialized manufacturer and exporter of sanitary material of non woven fabric and plastic films. Not only providing you with customized solutions, but also providing you with an incredible full range of end-to-end services to make everything easier.
- Superior Quality Control
- Compliance and Certification
- Innovative Product Development
- Cost Efficiency
- Sustainability Initiatives
- Reliability and Consistency
- Exceptional Customer Service
- Advanced Manufacturing Capabilities
- Performance and Innovation
- Transparent Communication
The FAQs About Plastic Film
Explore these common queries about spunbond nonwoven fabric. Contact us for further assistance!
Absolutely! Our team of expert provide OEM on request. We will work closely with you to ensure the material aligns with your application and meets your specific requirements.
We offer low MOQ standards to accommodate businesses of all sizes. Please contact us to discuss your specific requirements and we will provide you with a customized quote.
Absolutely! We provide samples to help you evaluate the quality and suitability of our plastic films for your application. Please contact us to request samples and discuss your specific needs.
Quality is ensured through stringent quality control processes, including regular testing for strength, durability, weight, and other key parameters. Our manufacturing facilities are equipped with advanced technology to maintain consistent quality across all batches.
Our team of experts is committed to providing excellent customer service and support throughout the entire process. If you have any questions or concerns after placing your order, please do not hesitate to reach out to us.
We have a robust supply chain management system and large-scale production capabilities to handle large orders efficiently. We work closely with our logistics partners to ensure timely delivery and provide regular updates on order status.
Don't hesitate contact with us, send mail
Contact us to get a free quote and more expertise about disposable underpad. Your project will meet a right solution with Medpos.
- We will contact you within 12 hours
- Don't worry, we hate spam too!